Weighbridge and industrial scale users are facing an uphill battle against low-priced, low-quality, sub-standard service from scale and calibration service providers. Accuracy and reliability problems, poorly maintained equipment, and regulatory compliance issues are the unwelcome outcomes.
A shortage of skilled technicians, companies closing or withdrawing from the market, rising costs, falling service quality, and unscrupulous providers are creating an untenable situation that must change.
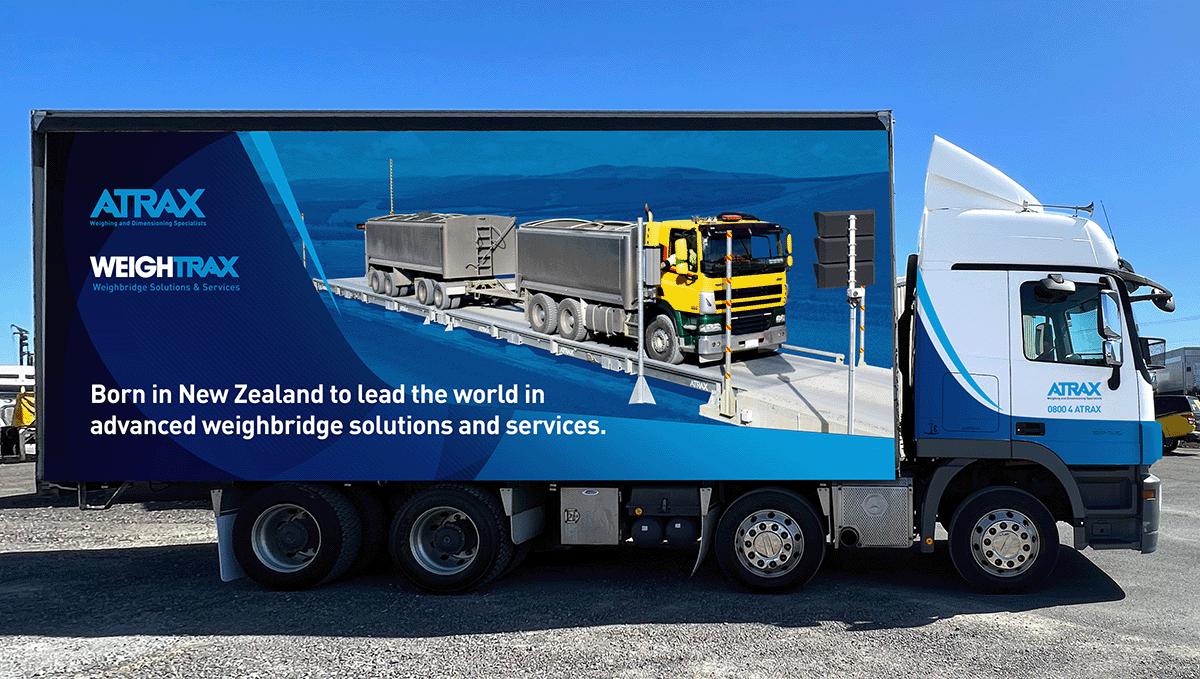
Atrax Group calibration truck coming soon to a weighbridge near you
Skilled staff shortages and service provider gaps
The need for high quality, competent service from trustworthy scale service providers has never been greater. However, there is a growing shortage of proficient scale technician staff, with many old school experienced tradesmen retiring or leaving the industry. In response, many scale service companies have either reduced their service, or have failed to perform – with significant consequences.
One public example of this: In May 2022 Precia Molen New Zealand Limited’s (Precia Molen) Weights & Measures Accreditation was cancelled. This follows the prosecution (under the Weights and Measures Act 1987) brought against Precia Molen earlier in 2022 by the Ministry of Business, Innovation and Employment (reported by the New Zealand Herald in an article dated 4 February 2022). Precia Molen was convicted of being deliberately in breach of the Weights and Measures Act 1987 after knowingly using the ‘wrong part’ to repair a weighbridge at Tegel Chicken’s New Plymouth plant. In court, Alistair Miller, lawyer for MBIE, said Precia Molen had opened Tegel up to potential criminal liability. The cancellation of Precia Molen’s Weights and Measures Accreditation means the company can no longer calibrate and issue Certificates of Accuracy for weighbridges and weighing equipment. In response, Precia Molen has purchased an independent calibration company to conduct this work on its behalf.
Another, unnamed, example is of a concrete company that was subjected to sub-standard service from a scale service company it thought it could trust. The concrete company had the scale service company calibrate its loadout hopper scales. It then went on to do a job pouring concrete, only to discover that the concrete strength was incorrect for the application. The concrete company later found out that the scales were wrong and had not been serviced properly, so the concrete components were incorrectly measured. As a result, the company had to dig up all the concrete that had been laid and fix it. This cost tens of thousands of dollars.
Then, there are service provider gaps caused by different factors. Independent New Zealand scale companies, like ScaleTec of Palmerston North, have sold up and their experienced technician owners have retired.
For larger multinational companies, prices for scale servicing and professional calibration in New Zealand are comparatively too low to allow for proper service and traceable calibration work, making it commercially unviable to continue. For example, a large multinational specialist weighing company decided to withdraw its truck scale division from New Zealand rather than compromise its service quality.
Rising costs, falling service quality
Adding to the perfect storm, the rising costs of labour, transport, fuel and more have put further pressure on scale service and calibration companies, many of which have responded by lowering the quality of the service they provide.
Regulatory compliance crackdown
At Trading Standards, the Government agency responsible for administering and enforcing the weights and measures legislation in New Zealand, there has been a subtle shift from education over to enforcement. The agency is increasingly more focussed on industry checking and corrective penalties, partly driven by the sub-standard or fraudulent activities it is finding in the market.
Government local bodies and industry agencies are requiring more measurement data reporting on a regular basis. This puts heavy emphasis on the need for accurate weighing, measuring, and recording.
Rising costs are also driving successful, quality companies to require better measurement data and tighter controls to maximise productivity and ensure profitability in their businesses.
Preventative maintenance: ‘She’ll be right’ approach is not alright.
Smart companies have also recognised the need for effective, regular, quality maintenance to protect their machinery assets and ensure longer life, increased uptime, and greater accuracy.
A ‘she’ll be right’ attitude, with poor maintenance from the lowest price, corner-cutting, unqualified service and calibration supplier is simply not good enough – and it never has been, but as the examples above show, the risk of prosecution, and the lost profits, are just too great to let this continue.
The way forward
So, what is the way forward? Businesses that use industrial scales and weighbridges need to be able to rely on the companies that they entrust with the critical task of supplying, servicing, maintaining, and calibrating their scales. And there are certainly trustworthy, accredited companies out there.
Look for credentials, and quality service and support.
The service may not be the cheapest on the market – but the value you get out of it over the long term will more than compensate.
It is more important than it has ever been that businesses can be confident in their scales and the service for those scales. Equipment costs are increasing and downtime costs businesses more every day. Good support and maintenance are the best way to extend the life of your investments.
Atrax Group has always recognised the need for good value, high quality maintenance and calibration services for weighbridges and scale systems. We have always invested in the best people and the best equipment and technology. Over the last year and a half, we have been increasing our capacity and investing heavily in skilled staff and resources to make sure our clients – current and prospective – can be guaranteed top-class products, systems, service, and support for years to come. We service and support all the equipment and systems we sell.
Ask for references. Word of mouth is often one of the best ways to find a trustworthy company. Many of our clients have come to us this way. Atrax Group currently supplies weighbridges, software and full weighbridge automation solutions and support services to 50% (and growing) of all local council waste sites throughout New Zealand.
In 2023, we expanded into the South Island of New Zealand following a merger with specialist weighing and scale products company MacWay Scales. Alongside offering industrial weighing and scale products, custom build solutions, repair service contracts, and accredited trade calibrations that complement our core offerings, MacWay, trading as Atrax South Island Limited, specialises in supplying and supporting marine motion-compensated scales and processing equipment for the fishing and food industries.
In 2024, we will have a weighbridge test truck on the road in the North Island, ready to visit sites on call for trade calibrations. Another test truck for the South Island is in the works.
Look for accreditations and certifications.
Is the scale company you want to use accredited and certified to carry out the work you need done? Are they compliant?
Atrax Group takes legal compliance and quality very seriously. Atrax Group clients can be confident in our processes and that they will be compliant when using our weighing and dimensioning products.
Atrax Group has a fully certified Integrated Management System. We are ISO 9000 accredited for quality, safety, and the environment (possibly the only industrial scale and weighbridge company in New Zealand that is ISO accredited in all three areas). We have approvals and certificates for measurement accuracy and equipment safety, from relevant government and independent testing agencies, for use in 160 countries.
Atrax Group is licensed by Trading Standards for trade measurement calibration and certifications. All test weights/measuring references used are traceable to the Trading Standards.
Organisations that need to meet specific compliance reporting requirements (such as New Zealand councils, which are subject to the requirements of the National Waste Data Framework), can be confident that our Weightrax weighbridge software will deliver the data they need to meet their obligations.
Last word…
Being able to trust and rely on the company that services and calibrates their scales and weighbridges enables businesses to do good business with their clients and meet profitability goals, while being compliant with regulations and reporting requirements. It’s worth its weight in gold – and it is something we must all demand.
About Kevin Maurice
Kevin Maurice is the founder and CEO of weighing and dimensioning specialist company Atrax Group. Kevin is responsible for the overall operations of Atrax Group, both in New Zealand and globally. He founded Atrax Group in 1986 and has grown the business internationally and locally into a world leading industrial weighing, measurement, and control systems operation with clients in 160 countries. As an engineer, Kevin lives and breathes the reliability and the accuracy Atrax Group’s devices and software. He takes great pride in the depth of experience Atrax Group has, and the high performance standards to which the company adheres.
Note: A version of this article was originally published in the January 2024 edition of Contractor Perspectives.